Folding the Future: How Origami Modules Are Redefining Construction
Yi Zhu, a Research Fellow in Mechanical Engineering, holds an origami design that is capable of folding up into something that could fit into a pocket and capable of expanding out into something much longer. Credit: Brenda Ahearn/University of Michigan, College of Engineering, Communications and MarketingFoldable origami with thick panels opens a world of possibilities.For the first time, engineers at the University of Michigan have shown that load-bearing structures, such as bridges and shelters, can be constructed using origami modules. These versatile components are capable of folding compactly and morphing into various shapes.It’s an advance that could enable communities to quickly rebuild facilities and systems damaged or destroyed during natural disasters, or allow for construction in places that were previously considered impractical, including outer space. The technology could also be used for structures that need to be built and then disassembled quickly, such as concert venues and event stages.Advancements in Origami Construction“With both the adaptability and load-carrying capability, our system can build structures that can be used in modern construction,” said Evgueni Filipov, an associate professor of civil and environmental engineering and of mechanical engineering, and a corresponding author of the study in Nature Communications. Principles of the origami art form allow for larger materials to be folded and collapsed into small spaces. And with modular building systems gaining wider acceptance, the applications for components that can be stored and transported with ease have grown.From left, Yi Zhu, a Research Fellow in Mechanical Engineering, and Evgueni Filipov, an associate professor in both Civil and Environmental Engineering and Mechanical Engineering, working in his lab in the George G. Brown Laboratories Building. Filipov and Zhu are applying principles of origami to create Modular and Uniformly Thick Origami (MUTO) for large-scale, load-carrying, adaptable structures. These can be used to create temporary structures such as stages or concert venues as well as to build structures such as buildings or bridges to be used in response to natural disasters. Credit: Brenda Ahearn/University of Michigan, College of Engineering, Communications and MarketingResearchers have struggled for years to create origami systems with the necessary weight capacities while keeping the ability to quickly deploy and reconfigure. U-M engineers have created an origami system that solves that problem. Examples of what the system can create include:A 3.3-foot-tall column that can support 2.1 tons of weight while itself weighing just over 16 pounds, and with a base footprint of less than 1 square foot.A package that can unfold from a 1.6-foot-wide cube to deploy into different structures, including: a 13-foot-long walking bridge, a 6.5-foot-tall bus stop, and a 13-foot-tall column.A New Approach to Origami DesignA key to the breakthrough came in the form of a different design approach provided by Yi Zhu, research fellow in mechanical engineering and first author of the study.“When people work with origami concepts, they usually start with the idea of thin, paper-folded models—assuming your materials will be paper-thin,” Zhu said. “However, in order to build common structures like bridges and bus stops using origami, we need mathematical tools that can directly consider thickness during the initial origami design.”Evgueni Filipov, an associate professor in both Civil and Environmental Engineering and Mechanical Engineering, demonstrates different folds and structures with a small model in his lab. Credit: Brenda Ahearn/University of Michigan, College of Engineering, Communications and MarketingTo bolster weight-bearing capacity, many researchers have attempted to thicken their paper-thin designs in varying spots. U-M’s team, however, found that uniformity is key.“What happens is you add one level of thickness here, and a different level of thickness there, and it becomes mismatched,” Filipov said. “So when the load is carried through these components, it starts to cause bending.“That uniformity of the component’s thickness is what’s key and what’s missing from many current origami systems. When you have that, together with appropriate locking devices, the weight placed upon a structure can be evenly transferred throughout.”In addition to carrying a large load, this system—known as the Modular and Uniformly Thick Origami-Inspired Structure system—can adapt its shapes to become bridges, walls, floors, columns, and many other structures.Reference: “Large-scale modular and uniformly thick origami-inspired adaptable and load-carrying structures” by Yi Zhu, and Evgueni T. Filipov, 15 March 2024, Nature Communications.DOI: 10.1038/s41467-024-46667-0U-M’s research has been helped along by use of its Sequentially Working Origami Multi-Physics Simulator (SWOMPS). It’s a simulator that accurately predicts the behaviors or large-scale origami systems. Developed at U-M, the system has been available to the public since 2020.The research was funded by the U.S. National Science Foundation and the Automotive Research Center.
Foldable origami with thick panels opens a world of possibilities. For the first time, engineers at the University of Michigan have shown that load-bearing structures,...
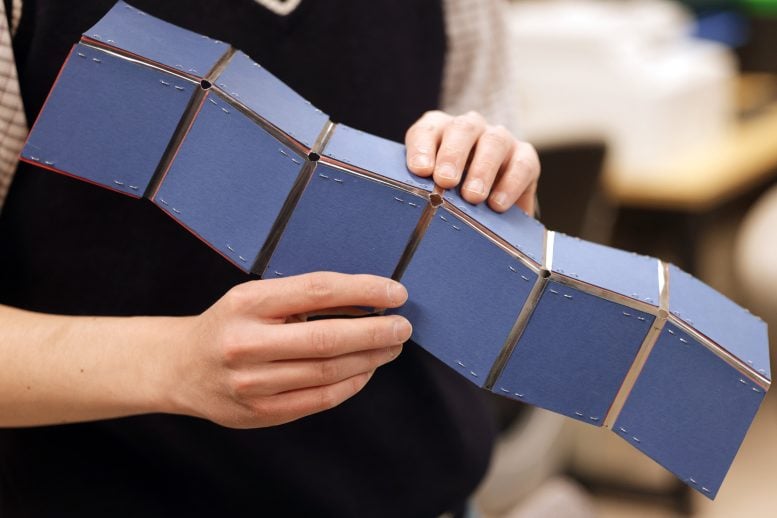
Yi Zhu, a Research Fellow in Mechanical Engineering, holds an origami design that is capable of folding up into something that could fit into a pocket and capable of expanding out into something much longer. Credit: Brenda Ahearn/University of Michigan, College of Engineering, Communications and Marketing
Foldable origami with thick panels opens a world of possibilities.
For the first time, engineers at the University of Michigan have shown that load-bearing structures, such as bridges and shelters, can be constructed using origami modules. These versatile components are capable of folding compactly and morphing into various shapes.
It’s an advance that could enable communities to quickly rebuild facilities and systems damaged or destroyed during natural disasters, or allow for construction in places that were previously considered impractical, including outer space. The technology could also be used for structures that need to be built and then disassembled quickly, such as concert venues and event stages.
Advancements in Origami Construction
“With both the adaptability and load-carrying capability, our system can build structures that can be used in modern construction,” said Evgueni Filipov, an associate professor of civil and environmental engineering and of mechanical engineering, and a corresponding author of the study in Nature Communications.
Principles of the origami art form allow for larger materials to be folded and collapsed into small spaces. And with modular building systems gaining wider acceptance, the applications for components that can be stored and transported with ease have grown.
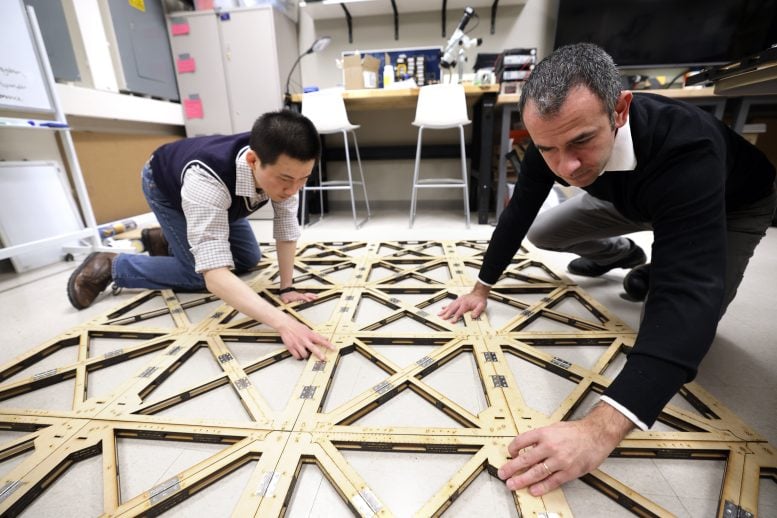
From left, Yi Zhu, a Research Fellow in Mechanical Engineering, and Evgueni Filipov, an associate professor in both Civil and Environmental Engineering and Mechanical Engineering, working in his lab in the George G. Brown Laboratories Building. Filipov and Zhu are applying principles of origami to create Modular and Uniformly Thick Origami (MUTO) for large-scale, load-carrying, adaptable structures. These can be used to create temporary structures such as stages or concert venues as well as to build structures such as buildings or bridges to be used in response to natural disasters. Credit: Brenda Ahearn/University of Michigan, College of Engineering, Communications and Marketing
Researchers have struggled for years to create origami systems with the necessary weight capacities while keeping the ability to quickly deploy and reconfigure. U-M engineers have created an origami system that solves that problem. Examples of what the system can create include:
- A 3.3-foot-tall column that can support 2.1 tons of weight while itself weighing just over 16 pounds, and with a base footprint of less than 1 square foot.
- A package that can unfold from a 1.6-foot-wide cube to deploy into different structures, including: a 13-foot-long walking bridge, a 6.5-foot-tall bus stop, and a 13-foot-tall column.
A New Approach to Origami Design
A key to the breakthrough came in the form of a different design approach provided by Yi Zhu, research fellow in mechanical engineering and first author of the study.
“When people work with origami concepts, they usually start with the idea of thin, paper-folded models—assuming your materials will be paper-thin,” Zhu said. “However, in order to build common structures like bridges and bus stops using origami, we need mathematical tools that can directly consider thickness during the initial origami design.”
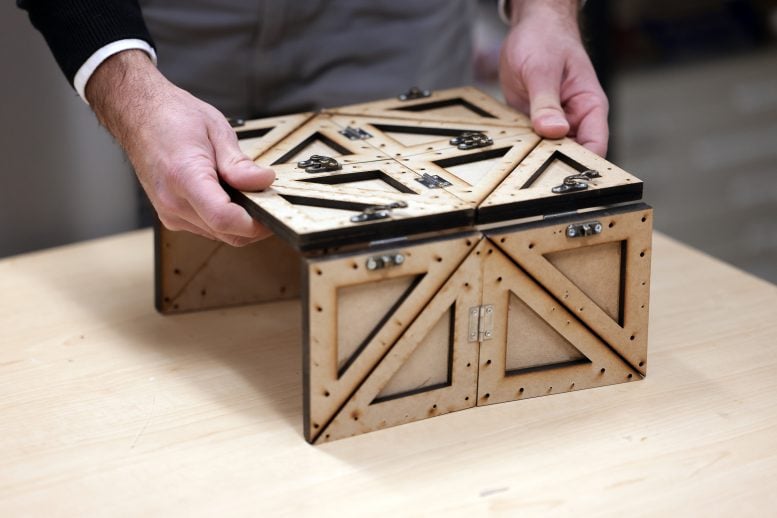
Evgueni Filipov, an associate professor in both Civil and Environmental Engineering and Mechanical Engineering, demonstrates different folds and structures with a small model in his lab. Credit: Brenda Ahearn/University of Michigan, College of Engineering, Communications and Marketing
To bolster weight-bearing capacity, many researchers have attempted to thicken their paper-thin designs in varying spots. U-M’s team, however, found that uniformity is key.
“What happens is you add one level of thickness here, and a different level of thickness there, and it becomes mismatched,” Filipov said. “So when the load is carried through these components, it starts to cause bending.
“That uniformity of the component’s thickness is what’s key and what’s missing from many current origami systems. When you have that, together with appropriate locking devices, the weight placed upon a structure can be evenly transferred throughout.”
In addition to carrying a large load, this system—known as the Modular and Uniformly Thick Origami-Inspired Structure system—can adapt its shapes to become bridges, walls, floors, columns, and many other structures.
Reference: “Large-scale modular and uniformly thick origami-inspired adaptable and load-carrying structures” by Yi Zhu, and Evgueni T. Filipov, 15 March 2024, Nature Communications.
DOI: 10.1038/s41467-024-46667-0
U-M’s research has been helped along by use of its Sequentially Working Origami Multi-Physics Simulator (SWOMPS). It’s a simulator that accurately predicts the behaviors or large-scale origami systems. Developed at U-M, the system has been available to the public since 2020.
The research was funded by the U.S. National Science Foundation and the Automotive Research Center.