Ultra-fast fashion is a disturbing trend undermining efforts to make the whole industry more sustainable
New Africa, ShutterstockSince the 1990s, fast fashion has enabled everyday people to buy the latest catwalk trends. But the sheer volume of garments being whipped up, sold and soon discarded is contributing to a global sustainability crisis. Now, just when the fashion industry should be waking up and breaking free of this vicious cycle, it’s heading in the opposite direction. We’re on a downward spiral, from fast fashion to ultra-fast fashion. The amount of natural resources consumed and waste produced is snowballing. Ultra-fast fashion is marked by even faster production cycles, blink-and-you’ll-miss-it trends, and poor labour practices. Brands like Shein, Boohoo and Cider are liberated from the concept of seasonal collections. Instead they are producing garments at breakneck speeds and self-generating microtrends such as balletcore, Barbiecore and even mermaidcore. At the same time there is limited transparency or accountability around clothing supply chains. The overproduction and consumption of clothing cannot be allowed to continue. Without change, the industry will account for 26% of the world’s carbon budget for limiting global warming to 2°C by 2050. The fashion industry must take responsibility for its actions. Policymakers also have an important role to play in enabling the necessary shift towards a more responsible and circular fashion economy. And let’s not forget the power of consumers. The dark side of Shein’s success (China Tonight, ABC News) Read more: To make our wardrobes sustainable, we must cut how many new clothes we buy by 75% Cheap clothing at what cost? It was once thought the pandemic would trigger a transition to a more sustainable fashion industry. Unfortunately in reality the industry is getting worse, not better. Most ultra-fast fashion brands emerged in the late 2010s following the most well known, Shein, founded in 2008. These online, direct-to-consumer brands exploded in popularity during lockdowns, with Shein holding the title of the world’s most popular brand in 2020. Established brands such as Gap introduce 12,000 new items a year and H&M 25,000. But Shein leaves them in the dust, listing 1.3 million items in the same amount of time. How is this even possible? The ultra-fast fashion model thrives on data and addictive social media marketing to create insatiable consumer demand. But Shein’s incredibly low prices (its website has thousands of items under A$5) come at a human cost. The company’s own 2021 Sustainability and Social Impact Report (later removed from the site) found only 2% of its factories and warehouses met its own worker safety standards, with the rest requiring corrective action. The brand has also forgone in-house designers. Instead it works with independent suppliers who can design and manufacture a garment in two weeks. The result is an incredibly profitable business model. Shein filed for an initial public offering (IPO) last year to value the brand at US$136 billion, up from US$2.5 billion in 2018. How Shein Built a $66B Fast-Fashion Empire (WSJ) Shifting from fast to ultra-fast fashion has serious environmental and social consequences. This includes even more exploitative labour practices. Shein garment workers reportedly work 75-hour weeks and warehouses operate 24/7. Ignoring this shift isn’t just a fashion faux pas. Doing so jeopardises national efforts for a more sustainable fashion industry. Read more: Fast Fashion: Why garment workers' lives are still in danger 10 years after Rana Plaza — Podcast A seamless transition to sustainability The Australian Fashion Council is leading a national product stewardship scheme called Seamless that promises to transform the fashion industry by 2030. The idea is to bring fashion into the circular economy. Ultimately that means zero waste, but in the meantime raw materials would be kept in the supply chain for as long as possible by designing out and minimising waste. Members will contribute a four-cent levy for every clothing item they produce or import. These funds go into clothing collection, research, recycling projects and education campaigns. BIG W, David Jones, Lorna Jane, Rip Curl, R.M. Williams, THE ICONIC, Sussan Group and Cotton On are Seamless Foundation Members. Each has contributed A$100,000 to the development of the scheme. As one of the world’s first industry-led collective product stewardship initiatives for clothing textiles, Seamless presents a unique opportunity to drive change towards a more sustainable and circular fashion industry. But there is a risk ultra-fast fashion brands may act as freeriders in Seamless, benefiting from the investment and initiatives without making meaningful contributions. Shein and others will continue putting more and more product on the market, which will need to be dealt with at the end of its short life. But if they fail to commit to the scheme, they won’t be the ones paying for that. The government-funded consortium must also recognise ultra-fast fashion in tackling the industry’s environmental and social sustainability challenges. At the moment they’re only talking about fast fashion and ignoring the rise of ultra-fast fashion. Their global scan, for example, includes a discussion of fast fashion and no mention of ultra-fast fashion. This also points to a lack of data more broadly in the industry but in the case of Seamless, it could have a big impact if this growing market segment is ignored. Shein and Temu are estimated to earn a combined $2 billion in sales in 2024, with customers from all walks of life. Read more: Fast fashion's waste problem could be solved by recycled textiles but brands need to help boost production The critical crackdown Some brands are actively engaged and working towards a more sustainable future. But others such as Temu are learning from Shein and looking to emulate their business model. The transition to a more sustainable and responsible fashion industry requires a greater understanding of ultra-fast fashion, urgent systemic changes and collective efforts. The Institute for Sustainable Futures, where I work, is a founding member of an international academic research network aimed at tackling the complexities of ultra-fast fashion. That includes how ultra-fast fashion is affecting the livelihoods of garment workers, how it’s fuelling textile waste and underscoring the industry’s struggle to embrace circular economy principles. We’re also investigating how to reshape consumer behaviour, away from social media-fuelled hauls towards more sustainable consumption particularly among Gen-Z consumers. Last month, Federal Environment Minister Tanya Plibersek announced a potential intervention, perhaps by introducing minimum environmental standards or a clothing levy by July. The clock is ticking. It is time to lay the foundation for a more sustainable and just fashion industry. Australia has a rich fashion history and is home to many leading local brands – many of whom have gone global. These brands show us what is possible when good design, sustainability and innovation drive an industry. Ultimately, our collective choices wield immense power. By understanding the consequences of our fashion habits and advocating for change, we can all be catalysts for a more sustainable and just fashion industry. Taylor Brydges is an Advisor to the Product Stewardship Centre of Excellence, which has provided mentorship to Seamless.
We know fast fashion is bad for the environment. Ultra-fast fashion makes matters worse. This disturbing trend towards disposable clothing is the opposite of sustainable. Here’s what must be done.
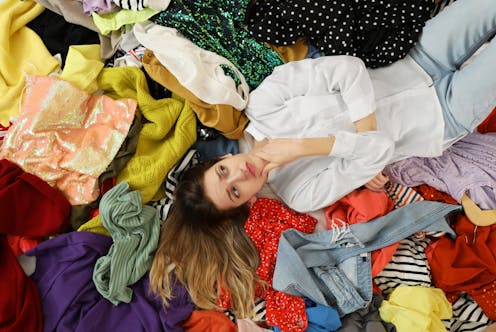
Since the 1990s, fast fashion has enabled everyday people to buy the latest catwalk trends. But the sheer volume of garments being whipped up, sold and soon discarded is contributing to a global sustainability crisis.
Now, just when the fashion industry should be waking up and breaking free of this vicious cycle, it’s heading in the opposite direction. We’re on a downward spiral, from fast fashion to ultra-fast fashion. The amount of natural resources consumed and waste produced is snowballing.
Ultra-fast fashion is marked by even faster production cycles, blink-and-you’ll-miss-it trends, and poor labour practices. Brands like Shein, Boohoo and Cider are liberated from the concept of seasonal collections. Instead they are producing garments at breakneck speeds and self-generating microtrends such as balletcore, Barbiecore and even mermaidcore. At the same time there is limited transparency or accountability around clothing supply chains.
The overproduction and consumption of clothing cannot be allowed to continue. Without change, the industry will account for 26% of the world’s carbon budget for limiting global warming to 2°C by 2050. The fashion industry must take responsibility for its actions. Policymakers also have an important role to play in enabling the necessary shift towards a more responsible and circular fashion economy. And let’s not forget the power of consumers.
Read more: To make our wardrobes sustainable, we must cut how many new clothes we buy by 75%
Cheap clothing at what cost?
It was once thought the pandemic would trigger a transition to a more sustainable fashion industry. Unfortunately in reality the industry is getting worse, not better.
Most ultra-fast fashion brands emerged in the late 2010s following the most well known, Shein, founded in 2008. These online, direct-to-consumer brands exploded in popularity during lockdowns, with Shein holding the title of the world’s most popular brand in 2020.
Established brands such as Gap introduce 12,000 new items a year and H&M 25,000. But Shein leaves them in the dust, listing 1.3 million items in the same amount of time. How is this even possible?
The ultra-fast fashion model thrives on data and addictive social media marketing to create insatiable consumer demand.
But Shein’s incredibly low prices (its website has thousands of items under A$5) come at a human cost. The company’s own 2021 Sustainability and Social Impact Report (later removed from the site) found only 2% of its factories and warehouses met its own worker safety standards, with the rest requiring corrective action.
The brand has also forgone in-house designers. Instead it works with independent suppliers who can design and manufacture a garment in two weeks.
The result is an incredibly profitable business model. Shein filed for an initial public offering (IPO) last year to value the brand at US$136 billion, up from US$2.5 billion in 2018.
Shifting from fast to ultra-fast fashion has serious environmental and social consequences. This includes even more exploitative labour practices. Shein garment workers reportedly work 75-hour weeks and warehouses operate 24/7.
Ignoring this shift isn’t just a fashion faux pas. Doing so jeopardises national efforts for a more sustainable fashion industry.
Read more: Fast Fashion: Why garment workers' lives are still in danger 10 years after Rana Plaza — Podcast
A seamless transition to sustainability
The Australian Fashion Council is leading a national product stewardship scheme called Seamless that promises to transform the fashion industry by 2030.
The idea is to bring fashion into the circular economy. Ultimately that means zero waste, but in the meantime raw materials would be kept in the supply chain for as long as possible by designing out and minimising waste.
Members will contribute a four-cent levy for every clothing item they produce or import.
These funds go into clothing collection, research, recycling projects and education campaigns.
BIG W, David Jones, Lorna Jane, Rip Curl, R.M. Williams, THE ICONIC, Sussan Group and Cotton On are Seamless Foundation Members. Each has contributed A$100,000 to the development of the scheme.
As one of the world’s first industry-led collective product stewardship initiatives for clothing textiles, Seamless presents a unique opportunity to drive change towards a more sustainable and circular fashion industry.
But there is a risk ultra-fast fashion brands may act as freeriders in Seamless, benefiting from the investment and initiatives without making meaningful contributions. Shein and others will continue putting more and more product on the market, which will need to be dealt with at the end of its short life. But if they fail to commit to the scheme, they won’t be the ones paying for that.
The government-funded consortium must also recognise ultra-fast fashion in tackling the industry’s environmental and social sustainability challenges. At the moment they’re only talking about fast fashion and ignoring the rise of ultra-fast fashion. Their global scan, for example, includes a discussion of fast fashion and no mention of ultra-fast fashion.
This also points to a lack of data more broadly in the industry but in the case of Seamless, it could have a big impact if this growing market segment is ignored.
Shein and Temu are estimated to earn a combined $2 billion in sales in 2024, with customers from all walks of life.
The critical crackdown
Some brands are actively engaged and working towards a more sustainable future. But others such as Temu are learning from Shein and looking to emulate their business model.
The transition to a more sustainable and responsible fashion industry requires a greater understanding of ultra-fast fashion, urgent systemic changes and collective efforts.
The Institute for Sustainable Futures, where I work, is a founding member of an international academic research network aimed at tackling the complexities of ultra-fast fashion. That includes how ultra-fast fashion is affecting the livelihoods of garment workers, how it’s fuelling textile waste and underscoring the industry’s struggle to embrace circular economy principles. We’re also investigating how to reshape consumer behaviour, away from social media-fuelled hauls towards more sustainable consumption particularly among Gen-Z consumers.
Last month, Federal Environment Minister Tanya Plibersek announced a potential intervention, perhaps by introducing minimum environmental standards or a clothing levy by July.
The clock is ticking. It is time to lay the foundation for a more sustainable and just fashion industry. Australia has a rich fashion history and is home to many leading local brands – many of whom have gone global. These brands show us what is possible when good design, sustainability and innovation drive an industry.
Ultimately, our collective choices wield immense power. By understanding the consequences of our fashion habits and advocating for change, we can all be catalysts for a more sustainable and just fashion industry.

Taylor Brydges is an Advisor to the Product Stewardship Centre of Excellence, which has provided mentorship to Seamless.